PoliceMonkey161
New member
Hello Gang....Ok so my last project was rebuilding an AMC 20rear end that I end up trussing out and stitch welded the tubes. Worked outgreat!(see the before and after below). I have put about 1000 miles on it, noproblems so far.
Now I'm moving on to the front end, I traded my old AMC 20rear for a slightly used Dana 30 (see photo). So far, I have it all torn downand started to clean off the 27 plus years of rust. If you have the time, Ihighly recommend re-building your our axles. It is time consuming, but oh sorewarding.......
and after.......... 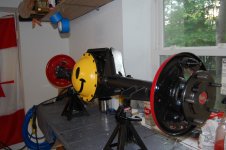
So here is the Dana......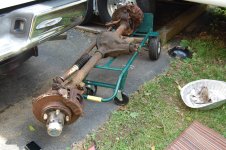
Now I'm moving on to the front end, I traded my old AMC 20rear for a slightly used Dana 30 (see photo). So far, I have it all torn downand started to clean off the 27 plus years of rust. If you have the time, Ihighly recommend re-building your our axles. It is time consuming, but oh sorewarding.......
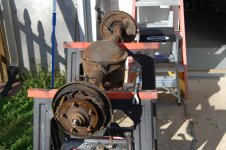
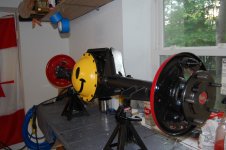
So here is the Dana......
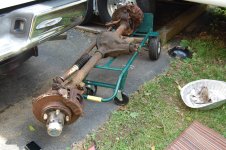