Ryan Kidder
New member
For those who have a Jeep frame (and structural under-body) rot problem (most typically the TJ’s), there is now a solution for those who don’t want to "junk" their Jeep!
A company now exists (in Avon, Indiana) which specializes in fixing the typical rust problems on vehicles (mainly Jeeps)! Although the prices are dependent on what all needs fixed; even the cost of all the "typical" repairs together are usually worth the investment (as those total costs would generally be less than half the price of a replacement "same year" Jeep, and ALL repairs are guaranteed for the life of the vehicle).
...that means a replacement frame section is guaranteed to NEVER rot out again!
-These rails are designed to interlock into the existing factory sections (front & rear), and are Tig welded (100% penetration) to join the sections!
The new rail sections were designed to eliminate the unneeded (factory) holes, but have added drain holes (within the front and rear "lower control arm frame brackets" to let the elements out!
-The skid plate frame "rivet nuts" are eliminated & instead replaced with weld-in style nut-assemblies which cannot fall out of the frame (even if for some near-impossible reason they ever came loose)!
-The side step frame "rivet nuts" are also eliminated and now replaced with another style weld-in nut so it doesn't spin loose if ever attempting to remove the bolts in the future, or to allow rust to form under them!
-All replacement sections are blasted, acid etched, and rustproofed (inside & out) with an extremely durable coating that is nearly as tough as the steel it is covering!
---------------------------------------
[[This coating isn't like a typical paint, as most "other" coatings mainly just "mechanically bond" to an objects outer surface.
To learn more, go to POR-15 Technical Information
Though, this is a professional coating/system which requires a certain level of expertise to make sure the process is effective. and those details will be covered in Post #4 (below) titled "Jeep Frame/Body-Rail Restoration (Por15 Process explained)"]]
---------------------------------------
That process extends at least 6” into the remaining factory “front” frame section, and extends at least 12” into the factory “rear” frame section! Though, the insides of the factory (remaining) sections are blasted/etched/coated as far as reachable (from the "cut" openings).
Blasted & Acid-Etched "Inner Rails" ("cut openings")

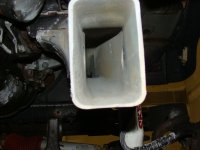
___
The rustproofing process can extend further for an additional cost, or can be completed by the owner to save money.
The coating can also be touched up by the owner assuming it ever gets damaged (sliding on rocks, etc).
------
Jeep owners from out-of-state who have no way of transporting their Jeep in for repair can have it shipped (through a broker) for typically between $500-$750.
“Prices” for some of these services can be found below in post #3…
------
Below are some pics of past Jeep frame and body rail repairs (before & after)...
Thanks!
Ryan Kidder/ Owner
Innovative Product Fabrication & Welding, LLC
-------
Those who have questions or comments should post below...
Those who are interested in these services can either call the number on the business post-card (in the last pic), or send a private message through the forums to trade contact info!
Call anytime between 10:00a - 10:00p, 7 days a week.
Business is currently “by appointment only”.
-------
2000 Jeep Wrangler (Severe Mid-Lower Frame Rot)
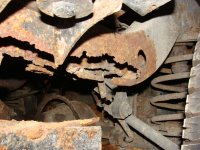
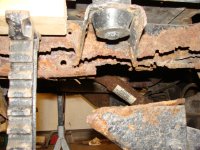
Notice the cut welds where the skid plate was welded to the frame... That is a typical sign that the Frame "Rivet Nuts" either started coming loose or had previously ripped out of the frame, and was an attempt to temporarily fix the problem.
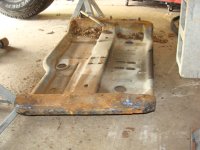
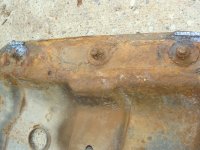
The customer also requested that the skid-plate be restored as well. In this pic, the old bolts/rivet nuts were removed, and the plate had been blasted & acid-etched (phosphatized)
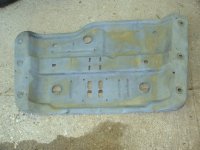
Fitting up the coated skid-plate to the rebuilt frame
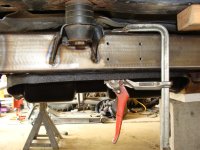
Completed (and Acid-etched) frame ready for coating
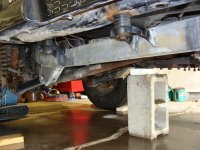
Jeep reassembled with Frame & Skid Plate Rustproofed
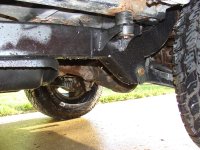
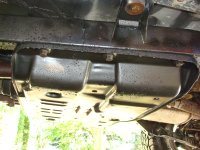
1999 Jeep Wrangler (Moderate Mid-Lower Frame Rot)
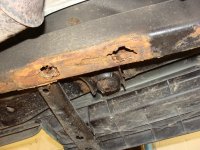
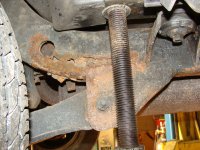
Body Rail Rot (Middle Mount)
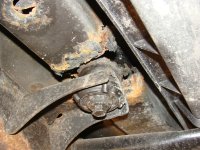
C-Notched Fit-up of "old" to "new" sections
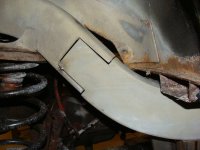
Replacement frame section welded into place
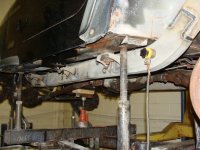
Rebuilt "body-rail mount" fit-up & ready to be welded into place
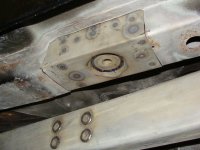
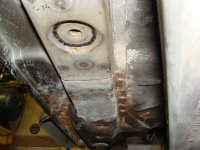
Rebuilt "body-rail mount" rustproofed
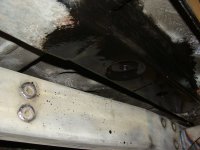
1 of 4 Added Frame Drain Holes (1 shown in "front" Lower Trailing Arm Mount Bracket)
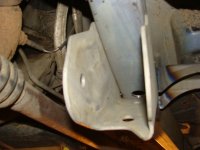
Replacement frame section freshly coated (inside & out)
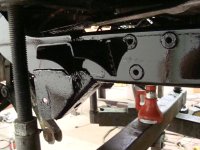
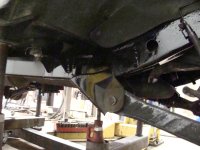

Business info
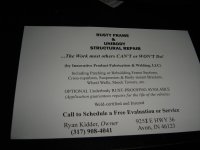
Call anytime between 10:00a - 10:00p, 7 days a week.
Business is currently “by appointment only”.
A company now exists (in Avon, Indiana) which specializes in fixing the typical rust problems on vehicles (mainly Jeeps)! Although the prices are dependent on what all needs fixed; even the cost of all the "typical" repairs together are usually worth the investment (as those total costs would generally be less than half the price of a replacement "same year" Jeep, and ALL repairs are guaranteed for the life of the vehicle).
...that means a replacement frame section is guaranteed to NEVER rot out again!
-These rails are designed to interlock into the existing factory sections (front & rear), and are Tig welded (100% penetration) to join the sections!
The new rail sections were designed to eliminate the unneeded (factory) holes, but have added drain holes (within the front and rear "lower control arm frame brackets" to let the elements out!
-The skid plate frame "rivet nuts" are eliminated & instead replaced with weld-in style nut-assemblies which cannot fall out of the frame (even if for some near-impossible reason they ever came loose)!
-The side step frame "rivet nuts" are also eliminated and now replaced with another style weld-in nut so it doesn't spin loose if ever attempting to remove the bolts in the future, or to allow rust to form under them!
-All replacement sections are blasted, acid etched, and rustproofed (inside & out) with an extremely durable coating that is nearly as tough as the steel it is covering!
---------------------------------------
[[This coating isn't like a typical paint, as most "other" coatings mainly just "mechanically bond" to an objects outer surface.
To learn more, go to POR-15 Technical Information
Though, this is a professional coating/system which requires a certain level of expertise to make sure the process is effective. and those details will be covered in Post #4 (below) titled "Jeep Frame/Body-Rail Restoration (Por15 Process explained)"]]
---------------------------------------
That process extends at least 6” into the remaining factory “front” frame section, and extends at least 12” into the factory “rear” frame section! Though, the insides of the factory (remaining) sections are blasted/etched/coated as far as reachable (from the "cut" openings).
Blasted & Acid-Etched "Inner Rails" ("cut openings")

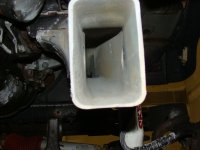
___
The rustproofing process can extend further for an additional cost, or can be completed by the owner to save money.
The coating can also be touched up by the owner assuming it ever gets damaged (sliding on rocks, etc).
------
Jeep owners from out-of-state who have no way of transporting their Jeep in for repair can have it shipped (through a broker) for typically between $500-$750.
“Prices” for some of these services can be found below in post #3…
------
Below are some pics of past Jeep frame and body rail repairs (before & after)...
Thanks!
Ryan Kidder/ Owner
Innovative Product Fabrication & Welding, LLC
-------
Those who have questions or comments should post below...
Those who are interested in these services can either call the number on the business post-card (in the last pic), or send a private message through the forums to trade contact info!
Call anytime between 10:00a - 10:00p, 7 days a week.
Business is currently “by appointment only”.
-------
2000 Jeep Wrangler (Severe Mid-Lower Frame Rot)
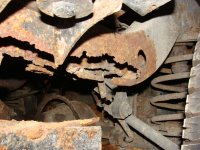
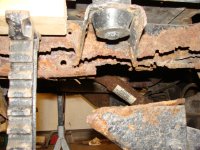
Notice the cut welds where the skid plate was welded to the frame... That is a typical sign that the Frame "Rivet Nuts" either started coming loose or had previously ripped out of the frame, and was an attempt to temporarily fix the problem.
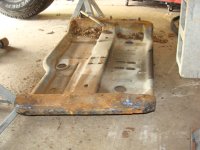
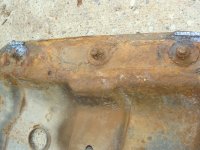
The customer also requested that the skid-plate be restored as well. In this pic, the old bolts/rivet nuts were removed, and the plate had been blasted & acid-etched (phosphatized)
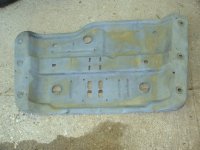
Fitting up the coated skid-plate to the rebuilt frame
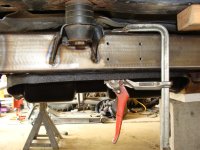
Completed (and Acid-etched) frame ready for coating
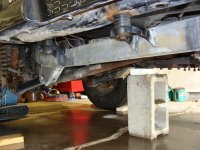
Jeep reassembled with Frame & Skid Plate Rustproofed
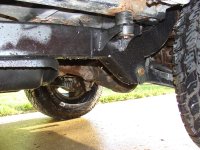
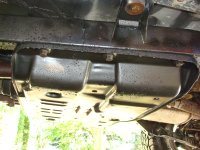
1999 Jeep Wrangler (Moderate Mid-Lower Frame Rot)
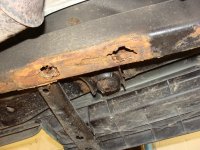
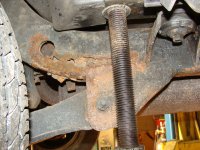
Body Rail Rot (Middle Mount)
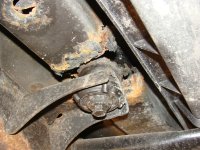
C-Notched Fit-up of "old" to "new" sections
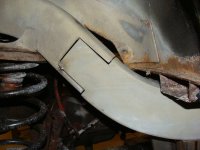
Replacement frame section welded into place
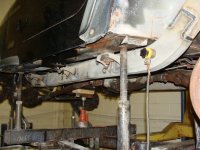
Rebuilt "body-rail mount" fit-up & ready to be welded into place
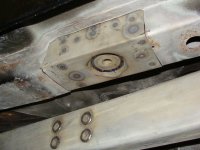
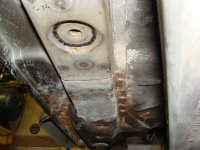
Rebuilt "body-rail mount" rustproofed
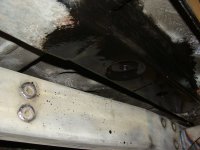
1 of 4 Added Frame Drain Holes (1 shown in "front" Lower Trailing Arm Mount Bracket)
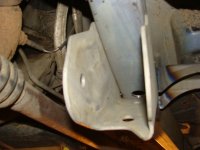
Replacement frame section freshly coated (inside & out)
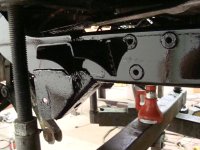
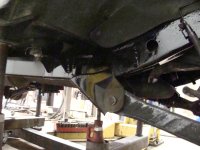

Business info
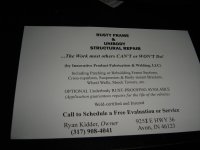
Call anytime between 10:00a - 10:00p, 7 days a week.
Business is currently “by appointment only”.
Last edited: